摘要 選用SiC作為骨料,長石和粘土組成的陶瓷結合劑和活性C作為成孔劑,對不同的燒成溫度下SiC多孔陶瓷的氣孔率和強度進行了研究。溫度的提高使SiC多孔陶瓷的顯氣孔率降低,而體氣孔率增大;氣孔形狀隨陶瓷結合劑的高溫性能變化而變化,1280℃燒成時的氣孔形狀多為圓形,尺寸分布較均勻;1240℃燒成時出現(xiàn)強度極大值,溫度提高使固體氣孔率增大而強度降低,但在大于1300 ℃時,由于SiC的高溫氧化產(chǎn)物參與晶界相反應,局部界面結合強度大大提高,使SiC多孔陶瓷瓷體強度異常增大。
ABSTRACT SiC powder as the backbone together with the ceramic binder composed of felspar mixed with clay and pore—forming c“rbon were chosen,several firing temperatures were experimented,and sonae pororities and strengthes of the po-rous SiC ceramics were analysed.The higher the firing temperature,the lower the bending strength as well as the lower the ap-parent porosity whereas the higher the body porosity in the porous SiC ceramics.The appearance of pores were determined by the high—temperature features of the binder.The pores tend to be spherical and more homogeneous at 1280℃.Due to the oxi-dation of SiC above 1300℃and that the oxided products will react with the boundary constituents.the local boundary strength was increased。which accounts for the abnormal increase of the strength of the porous SiC ceramics.
主題詞 SiC 燒成溫度 氣孔率 強度 晶界相
KEYWORD SiC firing temperature porosity strength grain boundary phase
1 引言
多孔陶瓷材料同其它多孔材料如多孔有機濾膜、玻璃纖維濾布等一樣可以應用于醫(yī)學臨床的病毒、細菌等微生物過濾,超濾分離血清蛋白;水資源過濾凈化及工業(yè)生產(chǎn)中的溶液(熔液)雜質(zhì)過濾和高溫煙塵過濾等,從而達到節(jié)約資源、保護環(huán)境的目的。對于較高壓力、較高溫度、較強腐蝕性等環(huán)境下的氣固分離或液固分離過濾過程中,多孔陶瓷材料具有無可替代的優(yōu)越性[1]。目前,國內(nèi)外對采用Al203(剛玉)、MAS(堇青石)、鈦酸鋁等為骨料的多孔陶瓷材料的研究已經(jīng)取得了一定進展[2,3],本實驗室選用SiC作為多孔陶瓷骨料和較低燒結溫度的結合劑,通過對SiC多孔陶瓷材料的氣孔率、氣孔形狀、強度等性能進行研究,結合SiC的高溫氧化特性,為提高SiC多孔陶瓷的強度等性能提出一些理論參考。
2 實驗過程
2.1 骨料粉體性能
本實驗選用超細SiC微粉為骨料,基本粒度約12μm,最大顆粒約28/μm,最小顆粒約4μm。選用活性炭作為成孔劑原料。活性炭高溫下燃盡產(chǎn)CO2,留下間隙,形成氣孔。選用長石—粘土為主要成分的陶瓷結合劑,其主要作用是高溫下熔融,產(chǎn)生玻璃相,將SiC骨料顆粒粘結在一起以提高多孔陶瓷的強度。實驗結果證明,瓷體的氣孔率與結合劑數(shù)量和燒成溫度有關[4]。
2.2 實驗方案
本實驗的工藝流程為:70%WT的SiC骨料微粉、15%WT的陶瓷結合劑和15%WT作為成孔劑的活性C粉混合;快速研磨4h(XM行星式球磨機);過篩;造粒;干壓成型;坯體干燥;燒成,燒成溫度分別為1160℃、1200℃、1240℃、1280℃、1320℃等,保溫時間均為2h。
多孔陶瓷的顯氣孔率用蒸煮法測得,體氣孔率通過排水法測定瓷體相對密度來確定,強度采用三點彎曲法測得。
3 實驗結果與討論
3.1 SiC多孔陶瓷的氣孔率
多孔陶瓷的顯氣孔率是指開口氣孔占材料總體積的百分率;而坯體內(nèi)氣孔總數(shù)(含開口氣孔)占總體積的百分數(shù)叫做體氣孔率。體氣孔率與瓷體相對密度有關,瓷體相對密度越大,體氣孔率越小。圖1是不同燒成溫度下SiC多孔陶瓷的顯氣孔率和密度變化結果。
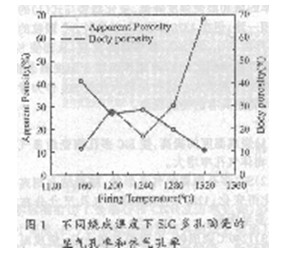
圖1 中曲線表明,隨著溫度的升高,多孔陶瓷的顯氣孔率減小,而體氣孔率增加。這種變化與陶瓷體內(nèi)結合劑的高溫熔融特性有關。
陶瓷結合劑是由長石和粘土組成的一組低共熔混合物,約在1200℃開始熔融。在1160℃的燒成溫度下,由于只在長石與粘土顆粒接觸的局部區(qū)域出現(xiàn)液相,陶瓷體內(nèi)不存在晶界玻璃相的粘性流動,成孔劑氧化揮發(fā)氣體沿坯體內(nèi)在成型過程中殘余的氣體通道向表面擴散,形成較多的開口氣孔(見圖2),表現(xiàn)出較高的顯氣孔率,此溫度下,陶瓷體內(nèi)的閉口氣孔含量很少,多為坯體成型過程中的殘余氣孔;燒成溫度變?yōu)?200℃時,陶瓷結合劑熔融,坯體內(nèi)出現(xiàn)晶界玻璃相的粘性流動,填充了部分氣孔通道,從而降低了顯氣孔率;溫度進一步升高時,玻璃相的粘度下降,流動性增加,更多的貫通通道被堵塞,顯氣孔率進一步下降;但是,晶界相粘性流動的增加使得坯體內(nèi)殘余氣體在擴散排除過程中不斷偏轉(zhuǎn)、閉合.形成閉氣孔。同時坯體膨脹,密度降低,體氣孔率相應增大。

因此,燒成溫度的提高降低了SiC多孔陶瓷的顯氣孔率,而使其體氣孔率增大。
3.2 SiC多孔陶瓷的氣孔形狀
多孔陶瓷的氣孔形狀、孔徑及分布直接影響著其實際應用效果。圖3是不同燒成溫度下樣品表面形貌圖。
圖3中顯示,1240℃燒成溫度下,樣品表面的氣孔尺寸分布不均勻,小氣孔在樣品表面出口處偏聚,形成較大尺寸開口氣孔,表面晶界相分布不均勻;1280℃燒成樣品開口氣孔多呈圓形,尺寸分布較均勻,存在大量結合劑熔融形成的晶界相,分布于SiC骨料顆粒之間; 1.320℃燒成時,樣品的晶界相完全呈玻璃態(tài),表面氣孔形狀不規(guī)則,尺寸分布趨于不均勻。

理論表明,由粘土、長石組成的系統(tǒng)中。在1240℃時長石部分熔融。形成新的莫來石相,但由于玻璃相粘度大,增大了氣孔排除阻力,在樣品表面偏轉(zhuǎn),沿表面缺陷處聚集,形成大的開口氣孔;溫度的升高使結合劑中莫來石相數(shù)量增加,石英溶解。結合劑形成的液相數(shù)量增加,逐漸出現(xiàn)高溫熔液的牯性流動,均勻地分布在骨料顆粒之間,將骨料顆料粘結在一起。高溫下成孔劑原料活性C氧化生成的CO2-氣體由體內(nèi)排除.在熔融玻璃相中形成氣孔通道,在樣品表面形成開口氣孔。根據(jù)表面張力及表面能有關理論,這樣形成的氣孔呈圓形,以維持最低的能量狀態(tài)”1;1320℃燒成時,燒成溫度的提高使結合劑的高溫熔融粘度下降,流動性增加,表面能和界面能下降,高溫液相與骨料顆粒表面的接觸角減小而使液相擴展,從而使氣孔形狀變形。
因此,SiC多孔陶瓷的氣孔形狀隨著結合劑高溫性能變化而變化。1280℃燒成時,氣孔分布較均勻,形狀多為理想的圓形。
3.3 SiC多孔陶瓷的強度
理論表明,多孔陶瓷的強度受陶瓷體內(nèi)氣孔率的影響[6];
σr=σ/σ0=exp(-np) (1)
式中:σr——多孔陶瓷的相對強度
σ0——致密樣品的強度(理論強度)
P——陶瓷體內(nèi)氣孔的體積分數(shù)(體氣孔率)
n——比例系數(shù),與結合劑類型、高溫熔融特性、晶界玻璃相與骨料顆粒之間的界面潤濕性等因素有關,一般為5~7。
由式(1)可知,多孔陶瓷的強度隨體內(nèi)氣孔率的升高而指數(shù)下降。根據(jù)圖1中氣孔率變化曲線,該實驗條件下,SiC多孔陶瓷的體氣孔率隨燒成溫度的升高而增大,因此強度應當逐漸降低。但是,實際實驗結果與理論出現(xiàn)了差異(如圖4)。

圖4不同燒成溫度下SiiC多孔陶瓷的強度變化
這種異常變化是陶瓷結合劑性能、坯體氣孔率以及骨料顆粒性能綜合作用的結果。
1160℃燒成時,由于結合劑未熔融,晶界相很少甚至不存在晶界玻璃相,不能將骨料顆粒粘結在一起而使其孤立分散在坯體內(nèi),因此強度很低;隨著溫度的提高,結合劑逐漸熔融,對SiC顆粒的粘結作用增強.從而使強度提高;到達1240℃時,由于坯體氣孔率最低(如圖1示)而使強度達到極大值;更高溫度下,由于坯體氣孔率的增加而使強度降低,變化趨勢與式(1)的計算結果相一致;但在1320℃下,由于骨料SiC顆粒的表面氧化,產(chǎn)生Si吼,而SiO2參與晶界反應。從而使SiC顆粒與晶界玻璃相之間的局部界面結合強度顯著提高,坯體強度異常增大。這種局部強化是SiC作為骨料的多孔陶瓷所具有的特殊現(xiàn)象。
4 結論
(1)燒成溫度的提高,使SiC多孔陶瓷的顯氣孔率降低,而體氣孔率增大。
(2)SiC多孔陶瓷的氣孔形狀,隨著結合劑高溫性能變化而變化;1280℃左右,開口氣孔尺寸分布較均勻,且多呈圓形。
(3)1240℃燒成時,出現(xiàn)強度極大值;燒成溫度的提高使多孔陶瓷的強度降低;而大于1300℃燒成時, SiC顆粒表面氧化使界面局部強化,陶瓷體強度顯著提高。
參 考 文 獻
1 沈君權.抗熱震多孔陶瓷在高溫煙氣干除塵方面的應用.工業(yè)陶瓷, 1990(1):12~20
2 史可順.多孔陶瓷制造工藝且進展,硅酸鹽通報,1994(3):20~38
3 劉陽、鄭乃章、陳虎爭.精陶骨料多孔陶瓷的研制.陶瓷研究.1998,13 (4):3~6
4 王連星、寧青菊、姚冶才.多孔陶瓷材料.硅酸鹽通報,1998(1):41~45
5 Kingery W.D.Bowen H.K.Uhlmann D.R .intuoduction to Ceramics,2nd edition,188~215
6 薛明值、劃智恩、沈凱.鈦酸鋁多孔琦瓷的研制.中國陶瓷,1995,31 (2):17~20